Supp-LIE Chain: How IoT is delivering TRUTH
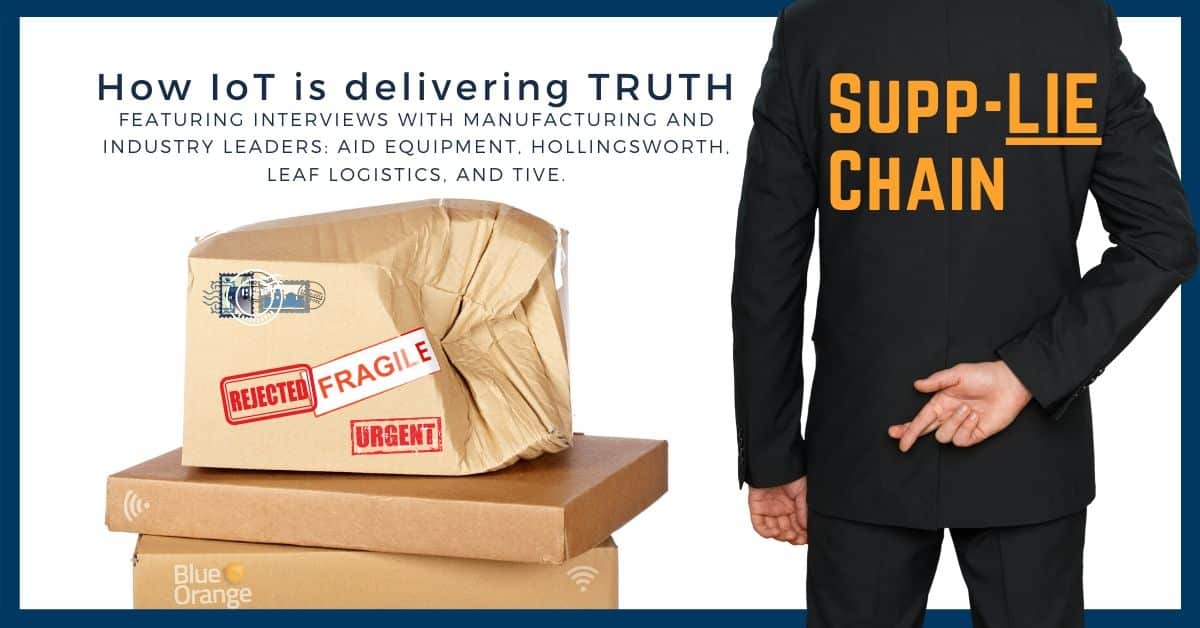
Featuring interviews with industry experts in automation and logistics on the innovations that increase accuracy and efficiency in Supply Chain: Aid Equipment, Hollingsworth, Leaf Logistics, and Tive.
The modern supply chain industry relies on a set of extremely powerful tools for keeping up with customer demand. Autonomous robots carry our products across warehouses. Sensors and trackers keep them under control, all the way from the conveyor belt to our doorsteps. The most common handheld scanners rely on advanced computer vision algorithms and OCR tools. NLP modules make human-robot communication easier than ever. The technical capabilities present in today’s supply chain were a thing of fantasy only a few decades ago.
And yet, it sometimes happens. A package gets lost. The wrong product gets delivered to a confused customer. Shipping is delayed by a few weeks. Something, somewhere along the supply chain goes wrong. Customers are dissatisfied, businesses lose revenue, and logistics partners waste time and resources.
This leaves warehouse managers wondering: “Where did it all go wrong? What can be done to prevent this from happening?” The following applications illustrate the role that different technologies play in alleviating some of the Supp-LIE chain issues.
Real-time Monitoring and Tracking
Monitoring and tracking technologies address an essential concern of warehousing operations: handling products is an error-prone process. Moreover, handling errors easily cascade through the entire supply chain pipeline and cause further costs at different points in time. The ultimate mistake happens once the wrong product has been delivered to the customer. “This isn’t what I ordered” is a painful thing to hear for all parties involved. Apart from unnecessary processing costs incurred all throughout delivery, customer satisfaction is also affected. Monitoring and tracking technologies help prevent such issues and are nowadays ubiquitous tools for inventory management.
Hollingsworth, a leading provider of third-party logistics services, relies on modern IoT and software technologies for real-time monitoring and tracking of products. RFID tracking is the core functionality of their inventory & shipping management systems.
“We use RFID tracking to ensure the accurate product is moving along the supply chain line. We also use a weight tracking service, so if someone says something is missing, we will notify the shipping provider.”
Alongside RFID capabilities, cloud technologies, and shipping management software are used to build task-based workflows. Like this, tracking data becomes available in real-time for both supply managers as well as customers. Knowing and acting on product location in real-time is the functionality that directly impacts the quality of their fulfillment services.
The company also relies on modern robotics for improving retail fulfillment operations. This enables them to automate tasks in order to reduce labor costs, minimize inefficiencies, and reduce overall operational costs.
Intelligent Conveyor Networks
Just as industrial automation plays a crucial role in the fourth industrial revolution, so is supply chain automation the driving force behind Supply Chain 4.0. From software to hardware, warehouse managers try to automate the most tedious tasks and delegate them to robots. By integrating AI, robotics, and IoT technologies, automation strategies become a powerful tool to minimize process flaws and optimize entire workflows.
Troy Harris, the co-owner of Aid Equipment, a factory design and install provider with over 40 years of industrial automation clarifies the importance and limits of smart device innovations:
“Now there are so many industrial-grade wireless technologies that are reliable, stable, and fast. This brings flexibility to our warehouses. Warehouse layouts are no longer tied to a pre-planned grid system with wide aisles for oversized equipment. Robots can simply track their own location and manage internal traffic to efficiently pick pieces for boxing.”
Aid Equipment’s conveyor networks integrate with computer vision capabilities, which enable barcode tracking systems to easily detect product identification tags and sort them.
“When you think of a robotic arm that sorts packages based on the scanned barcodes, it must be able to get information immediately in order to react within a millimeter of tolerance. The image capture rate plays a critical role in this when a conveyor system is running at 240 feet/minute and parts are coming by at 4 feet/second so there is limited time before the part gets skipped.”
Harris adds that computational power for these camera systems is also a limiting factor saying:
“A basic camera currently has the capacity to capture X and Y, or position and SKU, but unfortunately you can’t stack on too many other detections like color, size, and shape before eventually you run out of time to compute those features. The desire to detect more complicated features with one or more cameras increases the latency of the sorting arm where even a millisecond makes a huge difference in the overall production rate. More advanced cameras come at a cost and depending on the customer’s budget the ROI of the potential increase in speed may be worth it.”
Streamlined Shipping Operations
Sensor technologies have many applications outside the warehouse; they enable supply chain managers to keep track of products while they are in transit. However, the complexities of real-life loading and unloading scenarios require more than tracking and accurate scanning of assets. A well-known risk during cross-docking is that of products being lost, entirely damaged, or simply separated from their pallet. Without an exact location and historical transit data, it would be impossible to ever retrieve these products and they would remain lost forever. Sensors make such information easily available and data analysis tools can quickly parse real-time data flows, to alert about possible failures before they become catastrophic.
The CEO of Tive, Krenar Komoni, illustrates how they approached similar issues using advanced sensor technologies and 5G trackers:
“A web of smaller Bluetooth beacons on individual pallets feed information to the 5G tracker device that tracks the shipment as a whole. From this, you are able to tell if any pallets ever get separated from the pack, are forgotten or misplaced. Additional location accuracy lets you pinpoint each shipment and send notifications of misplaced items before the truck gets 5 miles away like standard trackers.”
Tive’s 5G trackers are only one component of their solution. They also offer advanced analytics to interpret heterogeneous data, such as location, environmental conditions, and transit events. Like this, all parties involved have a transparent overview of the shipping process and contribute to risk minimization.
Predictive Demand Mapping
Data analytics offers a reliable way to deal with uncertainty in the supply chain. The complex nature of supply chain events and actions makes it imperative to model, evaluate, and understand uncertainty. To illustrate, the possibility of customers returning a product may be influenced by a number of factors. Delivery times, competition prices, or faulty products may each play a role in the customer’s decision to return a product. Understanding customer expectations based on previous purchasing data brings transparency to the entire supply chain. This is exactly what data analytics tools are built to achieve: reduce uncertainty and increase customer satisfaction.
Leaf Logistics CEO, Anshu Prasad, gives further details on return issues in today’s supply chain:
“Today e-commerce has a 30% return rate and supply chain isn’t built for it […] the future of supply chain will require an integrated return system that must have pre-made options, systems, and routes for returns so the return experience is just as painless as the buying experience.”
Leaf provides a prescriptive analytics platform that enables companies to take a proactive attitude in supply chain management. Instead of using technology to react to events in the past, predictive demand mapping allows decision-makers to see into the future and make informed decisions.
“Supply chains need to optimize for close-loop systems, which will not only increase customer satisfaction but also sustainability. Less time with products sitting around ensures a quicker return to the manufacturer to be able to resell or repurpose the returned product.”
This is by no means an isolated use case for data analytics in the supply chain industries. Companies of all sizes find data-driven solutions increasingly affordable and secure. Predictive analytics makes it straightforward to find areas of improvement in the supply chain, stay productive, and cut down on operational costs.
Conclusion
IoT and automation have many applications in the supply chain industry. They enable a wide number of applications, from manufacturing, packaging, to delivery tracking, and the generation of automated reports.
Despite all these tools, the modern supply chain is still seeing constant development. Technologies such as computer vision, natural language processing, or predictive modeling open up new opportunities for countless applications. Successful integration and adoption of these new innovations and of existing systems is key to a full digital transformation, for this, it is recommended to partner with data transformation experts, like Blue Orange Digital, a top-ranked AI co-development agency. When high-performing algorithms take care of time-consuming, labor-intensive tasks, organizations can overcome process limitations, stay competitive, and increase the quality of their services.
Originally Published at: Data Drive Investor